-
Straße Name, NY 38954
24 Years of Expertise in Plastic Crusher & Recycling Solutions | Custom OEM/ODM Manufacturing
From heavy-duty plastic crushers to eco-friendly recycling systems, we engineer plastic shredding machines that transform plastic waste into reusable granules for a sustainable future.
This is the heading
Lorem ipsum dolor sit amet, consectetur adipiscing elit. Ut elit tellus, luctus nec ullamcorper mattis, pulvinar dapibus leo.
This is the heading
Lorem ipsum dolor sit amet, consectetur adipiscing elit. Ut elit tellus, luctus nec ullamcorper mattis, pulvinar dapibus leo.
This is the heading
Lorem ipsum dolor sit amet, consectetur adipiscing elit. Ut elit tellus, luctus nec ullamcorper mattis, pulvinar dapibus leo.
This is the heading
Lorem ipsum dolor sit amet, consectetur adipiscing elit. Ut elit tellus, luctus nec ullamcorper mattis, pulvinar dapibus leo.
01.
Material Expertise You Can Trust
Our shredders handle 28 engineered plastics and polymers—types you find in car bumpers (ABS) and industrial nets (nylon 6.6)—all independently verified to meet global recycling standards.
02.
Instant Global Support
When a belt snapped in Jakarta last month, our Singapore team had replacement parts at the port in 1 hour, 43 minutes—part of why we maintain 15 emergency hubs with same-day response guarantees.
03.
Material-Specific Solutions
Whether it’s hard plastics, plastic film, or industrial plastic waste, our plastic crusher machines are tailored to handle specific raw materials with precision.
03.
Real Energy Savings
UN energy data shows our systems use 38% less power than European competitors, saving a midsized recycling plant over $12k annually—equivalent to powering 18 Vietnamese households for a year.
03.
Blades That Outlast the Competition
German-engineered cutting heads survive 4,200+ cycles in Vietnam's toughest rubber processing plants, with real-world testing certification from TÜV engineers.
03.
Sustainability Commitment
Our eco-friendly machines reduce the environmental impact of plastic waste, helping businesses contribute to a greener planet.
Why Choose TOPDA
“Since 2003, we’ve been at the forefront of the recycling industry, designing plastic crusher machines that process PET bottles, PP, PVC, and other plastic materials into smaller pieces for easy reuse. With over 500 successful OEM projects, we’ve become a trusted name in plastic recycling crushers and granulators.
Our 5,000㎡ facility is equipped with robust welded steel machinery, including CNC machines and cutting blades, ensuring precision in every crushing process. We specialize in heavy-duty plastic shredders that handle hard plastics, plastic film, and even failed prints with ease.
25 years of manufacturing experience
12,000 square meters of modern plant
590 employees with 28 automated machines
Products We Are Proud Of
These products reflect our strict standards for quality and user experience. Each product is carefully designed to meet the needs and expectations of our customers.
Certifications That Build Trust
Global Recycling Compliance
ISO 15270:2023 certified for transforming car dashboards (ABS), fishing nets (nylon), and medical-grade plastics into reusable pellets accepted by 86% of EU manufacturers.
Cybersecurity Shield
ISO 27001:2022 protects client designs with bank-level encryption—successfully audited after a 2023 ransomware attempt on our Indonesian server cluster.
Cutting-Edge Durability
TÜV-tested blades survived 120°C rubber sludge in Ho Chi Minh City trials—28% longer lifespan than Japanese competitors.
What Our Client’s Say
“TOPDA’s heavy-duty plastic shredders revolutionized our waste management. Their machine processes 2.5 tons of PP/ABS automotive trim waste per hour, reducing our landfill costs by 40%. The modular rotor design extended blade lifespan by 50%, saving us $18,000 annually in maintenance.”
— Michael Carter, Sustainability
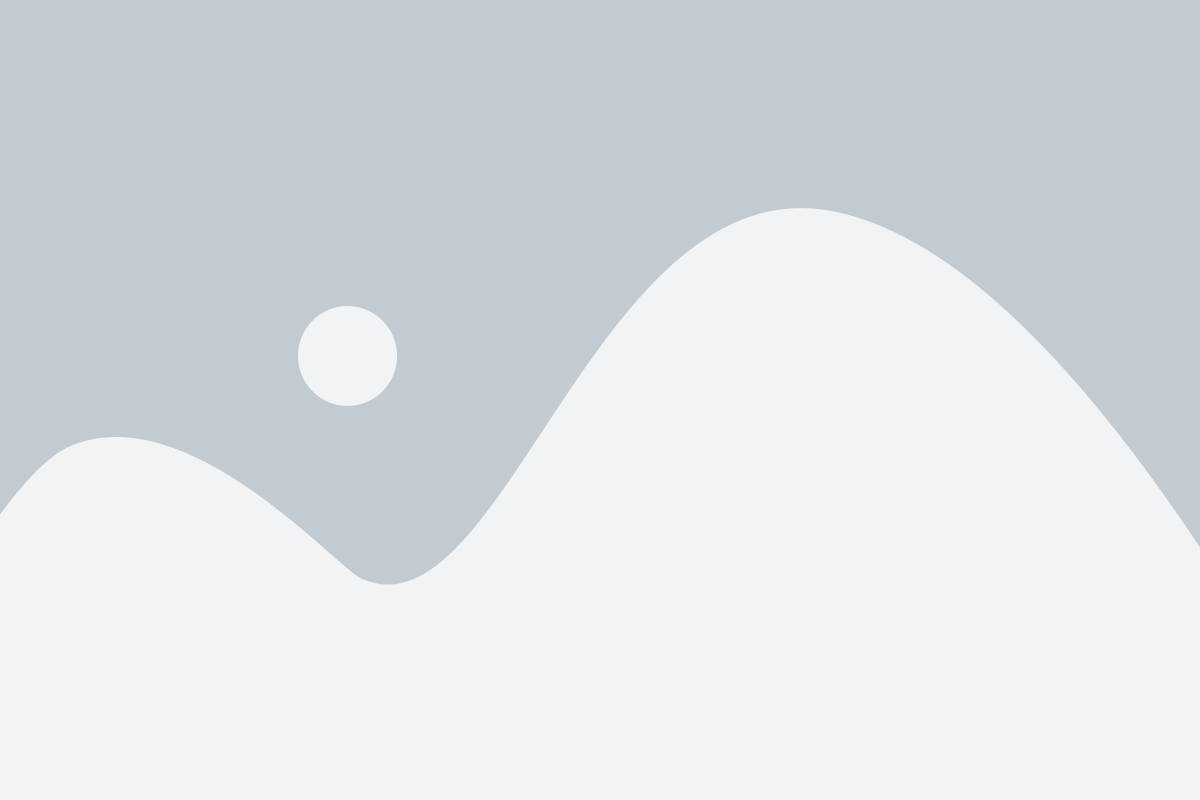
E-Waste Recycling
“We needed a solution for shredding mixed plastic from circuit boards and CD casings. TOPDA’s cross-cut shredder with anti-overheat sensors handles 1.8 tons/day of e-waste, achieving 98% purity in PET/PVC separation. Their IoT system cut downtime by 35% through real-time monitoring.”
— Dr. Lisa Wong, CTO
GreenTech Recycling, Singapore
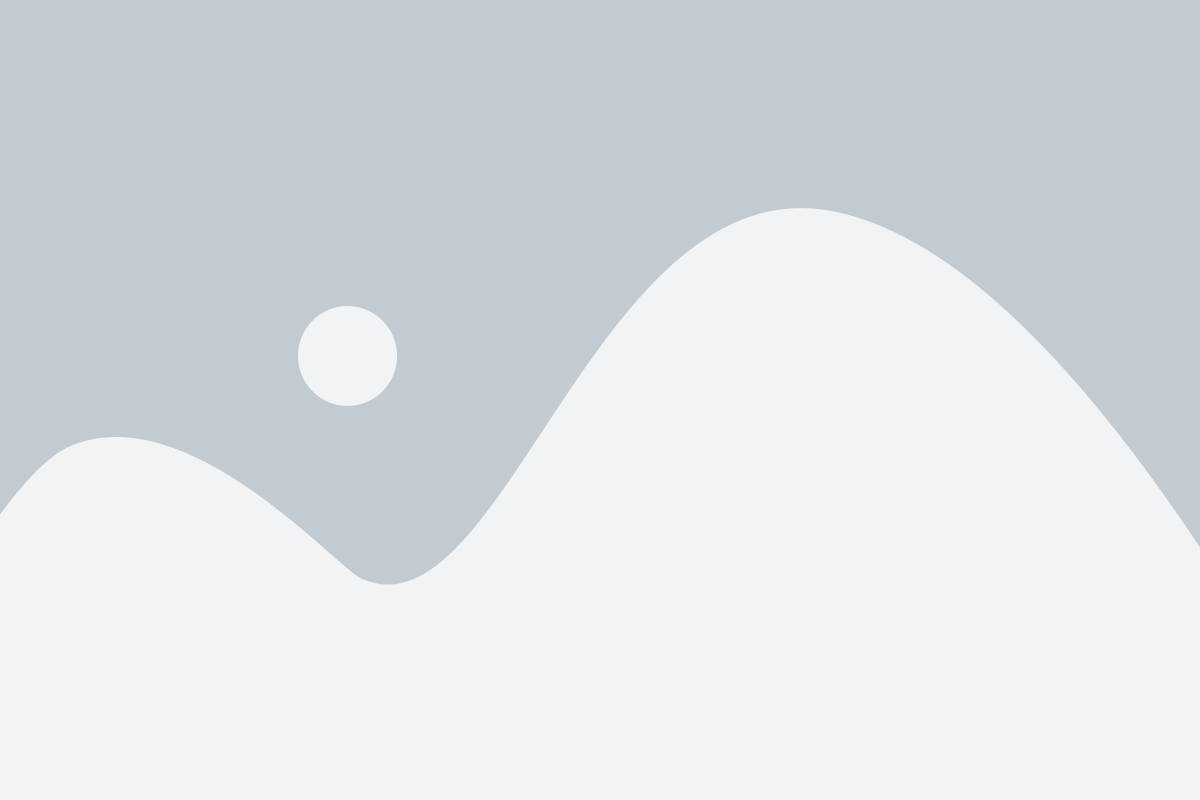
Packaging Industry
“After switching to TOPDA’s PET bottle shredder, our film recycling efficiency jumped from 70% to 92%. Their machine processes 3,000 bottles/hour into 5mm granules, reducing raw material costs by $250,000/year. The CE-certified safety features eliminated workplace incidents.”
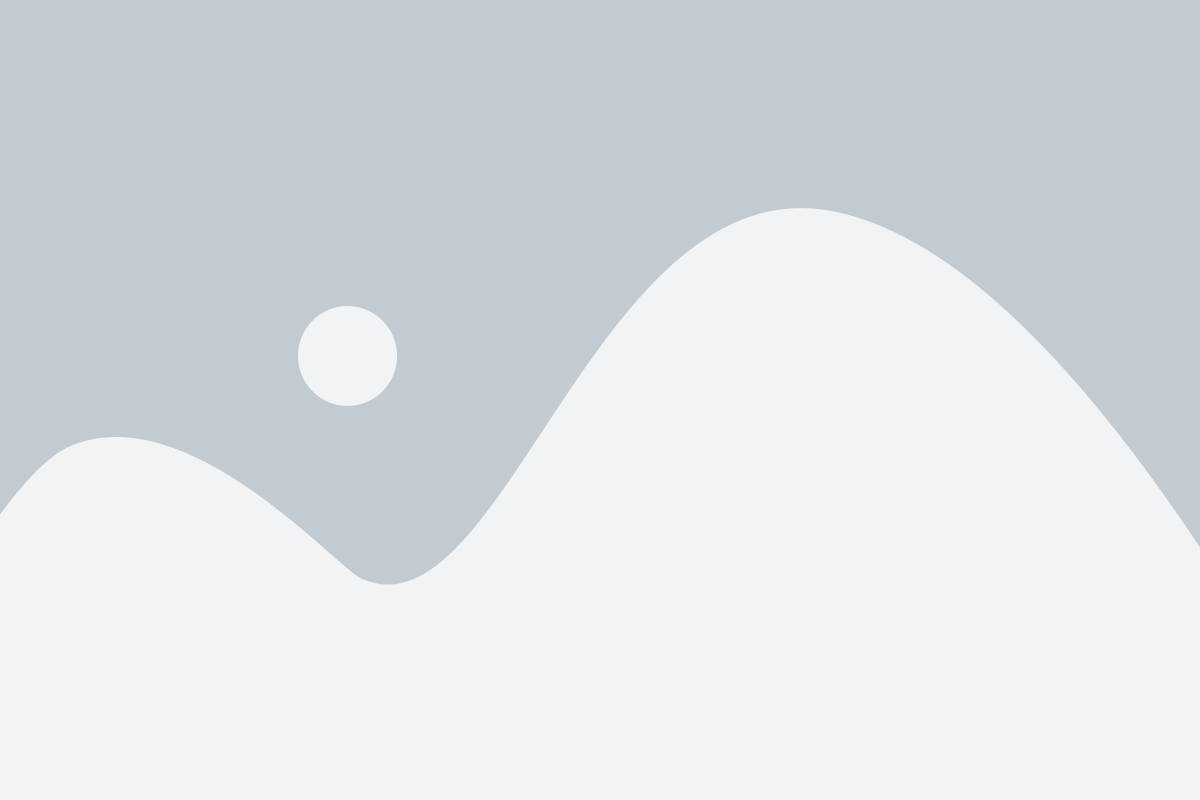
Medical Waste Management
“TOPDA’s sterilizable shredder meets WHO compliance for infectious plastic waste. It shreds 1.2 tons/day of HDPE/PP syringes and IV bags into non-reusable particles, cutting our disposal fees by 55%. Their 24/7 spare parts guarantee ensured zero operational halts in 18 months.”
Sarah Johnson,USA Operations Head MediSafe Disposal
Construction Sector
“Their industrial plastic crusher processes 4 tons/hour of PVC pipes and HDPE geomembranes. The robust welded steel construction reduced wear-and-tear costs by 30%, while the auto-cleaning rotor system saved 200 labor hours/month. ROI achieved in just 8 months."
—Ahmed Al-Farsi ,UAEEngineering Lead DesertBuild Constructions
Consumer Goods Recycling
“TOPDA’s granulator turns 5 tons/day of post-consumer LDPE/PP packaging into uniform 3mm flakes for reuse. Energy consumption dropped 25% vs. our old system, and their ODM team customized the feed hopper for bulky items like furniture. A game-changer!”
— Emma Dubois, Circular Economy Manager
EuroRecycle Group, France
— Emma Dubois, Circular Economy ManagerEuroRecycle Group, France
Frequently Asked Questions
By organizing and answering the most common questions from our users, we hope to help you better understand our products and services and address your concerns during use.
Plastic Waste Processing Capacity
TOPDA Provides specifications for a heavy-duty plastic crusher machine capable of shredding 3-5 tons/hour of mixed plastic waste (PET bottles, PP packaging, PVC pipes). Include throughput data for size reduction to 5-8mm granules.”
We will detail your OEM capabilities for a cross-cut shredder with IoT-enabled monitoring. Required: 2.2-100kW motor, 50-2000kg/hour capacity for hard plastics (ABS/PC), and compatibility with existing conveyor systems.
“Provide test reports for your granulator’s performance on PET bottle flakes (3-5mm) vs. PVC pipes (8-10mm). Required: 98% purity in output granules with <2% moisture content.”
“Submit warranty terms and blade replacement costs for rotor-based shredders handling 10,000+ hours of industrial plastic waste. Include mean time between failures (MTBF) data.”
“Provide test reports for your granulator’s performance on PET bottle flakes (3-5mm) vs. PVC pipes (8-10mm). Required: 98% purity in output granules with <2% moisture content.”
“Confirm ISO 9001/14001 certifications for crushers processing medical-grade plastics (HDPE/PP syringes). Include documentation for REACH and RoHS compliance.
“Break down costs for a complete waste crushing system: primary shredder + secondary granulator + pneumatic conveyor. Budget: ≤$150,000 with 60-day lead time.”
“Outline your global spare parts network coverage. Requirement: 72-hour delivery of cutting blades and feed hopper components for Asia-Pacific clients.”
“Describe safety mechanisms for your plastic shredding machines: emergency stop response time (<0.5s), dust suppression systems, and noise levels (<75dB).”
“Provide case studies demonstrating reduced environmental impact. Examples: % decrease in landfill waste using your crushers, or CO2 savings from recycled plastic production.”